- Decarbonization in buildings involves both operational changes, like switching to electric systems powered by renewable energy, and material choices that reduce embodied carbon.
- This holistic approach can lead to innovative, flexible, and sustainable workplace environments.
- Financial strategies for decarbonization must consider long-term investments that balance immediate costs with future savings and regulatory compliance, emphasizing the importance of durability and lifecycle costs in building materials and systems.
This article was written by Doug Davenport of ProspectSV, David Kaneda of IDeAs Consulting, and Pauline Souza of WRNS Studio for Work Design Magazine.
Decarbonized buildings represent a frontier in building development and an opportunity to rethink how they’re designed moving forward, opening new doors to think about how buildings can function. Turning points like decarbonization can redefine buildings for the better, and the design process follows suit. Workplace design is human-centric, bringing together elements of movement, function, productivity, corporate culture, and much more. What runs the building is hardly the most tangible aspect of an occupants’ experience.
Buildings represent more than 40% of U.S. carbon emissions, and natural gas-fired HVAC, water heating, cooking, and other systems represent the largest fraction. With a growing profile of electric HVAC, water heating, and cooking products entering the market, the Building Decarbonization industry is coming. Yet, this is just a fraction of the total carbon emissions represented in the materials, construction, and operation of commercial buildings.
How does this reflect the future of Workplace?
Decarbonization is a process of optimization and elimination. For example, we can replace carbon-emitting equipment in building systems (like natural gas-fueled HVAC and water heating) with electric equipment that runs on renewable energy, while also reducing “embodied carbon” through thoughtful choice of building materials, furnishings, and other internal features. Embodied carbon accounts for the global warming impact of carbon emitted from manufacturing and transporting materials for buildings.
We think this should happen in the following ways:
Design for Decarbonization
In working toward a zero-carbon workplace, we have an opportunity to innovate by delivering flexible, smart, carbon-free workplace environments. Not only are technology innovations making buildings more flexible, more responsive to management, and more interactive with occupants, but they are also deeply sustainable. The market for zero carbon workplaces will be driven by fresh approaches to building renovation and improvements and to efficient energy use by occupants. This will include minimizing energy use throughout the building via offset by P and battery systems and seeking reliable alternatives to traditional materials, ranging from concrete to fabrics. The deeper we go, the greater the opportunities.
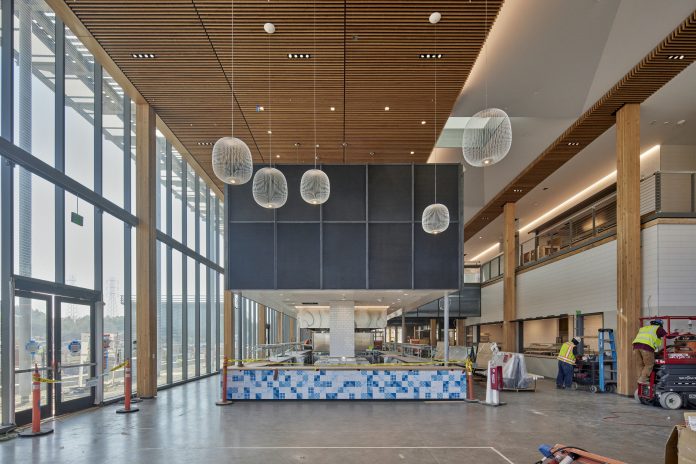
Fiscal Planning
Realizing the full value of decarbonization requires big-picture, rational financial thinking and long-term planning. Owners need a capital/investment roadmap for the short to medium term, which extracts the maximum possible savings at the highest possible yield on an owner’s investment. Lower utility expenses, lower maintenance/repair expenses, and greatly increased building comfort (along with satisfied tenants) maximizes return on investment and building value over time. Same is true for choice of furnishings and finishes: managing carbon reduction against durability and lifecycle cost is critical. These measures are not only a hedge against future cost of energy and regulation, but they also offer room within a project budget to accommodate deeper carbon reductions over the investment horizon.
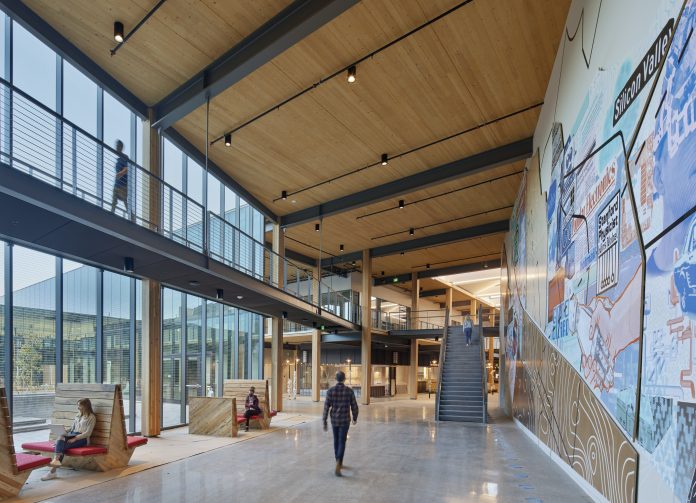
According to Paula Melton of BuildingGreen, “By 2050, the interior design industry will have influence over almost one-tenth of the world’s carbon emissions.” According to the United Nations Environmental Programme embodied carbon of building materials accounts for nearly 11% of GHG emissions. While seemingly a small percentage, it is the criticality of this moment that makes this a serious piece of the pie to reduce. As reported by Architecture 2030, in order to stay within the 1.5 degrees warming threshold, we need to reduce our embodied carbon by 65 percent by 2030 and 100 percent by 2040 – only 17 years away. The emissions we produce between now and 2050 will determine success or failure. This means there is a critical piece of the process that requires carbon literacy.
While tracking embodied carbon has been integrated into more design teams’ processes, the target of “better” or benchmark is understandably still evolving given the complexity of interiors. However, there are still ways to respond to the call for action – minimizing material deployment, reducing waste during procurement and installation, and selecting materials considering Environmental Product Declarations. If renovations typically happen every 3-8 years, we must consider every material as a bank for long term use or reuse right now. As products replace current carbon-intensive materials, we anticipate costs to trend downward; meanwhile, we need to consider where – and where not to – spend our material carbon capital.
Case Study – Microsoft Silicon Valley Campus
Projects like Microsoft’s Silicon Valley Campus (SVC) campus is an example of how design teams can employ a holistic approach that looks at every aspect of design to find strategies to reduce carbon.
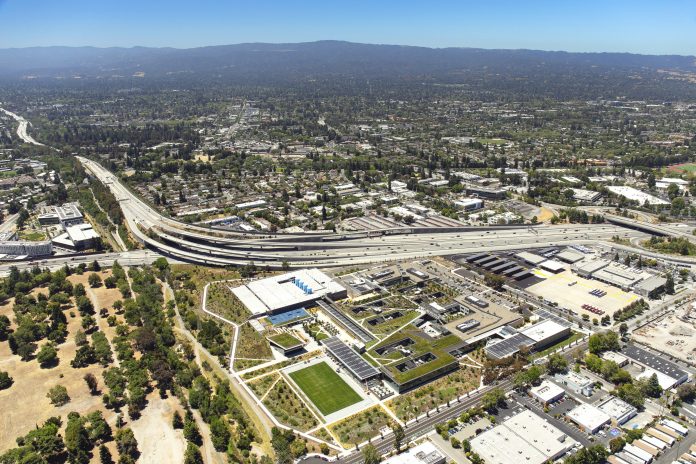
At Microsoft SCV, the WRNS Studio and their design team: invested in resilient strategies like a blackwater system, thermal storage, and photovoltaics; designed with reduced carbon through reuse and mass timber; and placed wellness, equity, and community front and center. Healthy, low-carbon material selection and sourcing drove systems and interior and exterior material design choices.
Microsoft’s commitment to the circular economy and carbon reduction informed the decision to reuse two existing buildings, as well as the selection of mass timber. The existing building provides 36% of the new campus footprint, accounting for a 28.6% reduction in total embodied carbon. With the project’s two floors of mass timber, the embodied savings increases to approximately 36% with an estimated total of 372 kg CO2e/m2. With over 345,000 square feet or 2,400 tons of 100% FSC cross laminated timber (CLT) panels, the wood reflects biophilic principles and a reduced carbon mission. The project is one of the largest CLT projects in North America.
Through tracking our carbon on past tenant improvements, WRNS can see that they generally break into four almost equal buckets of carpet, gypsum wallboard, workstations, and then everything else. While more refinement and understanding is required, it is clear that interior design and tenant improvement will be key areas of opportunity for lower carbon spending.